A colaboração com fornecedores chineses avançados de tubos de alumina reduz os prazos de entrega de protótipos em 35%, em média, aproveitando o suporte de engenharia para dimensionamento rápido e integração confiável do sistema de automação.
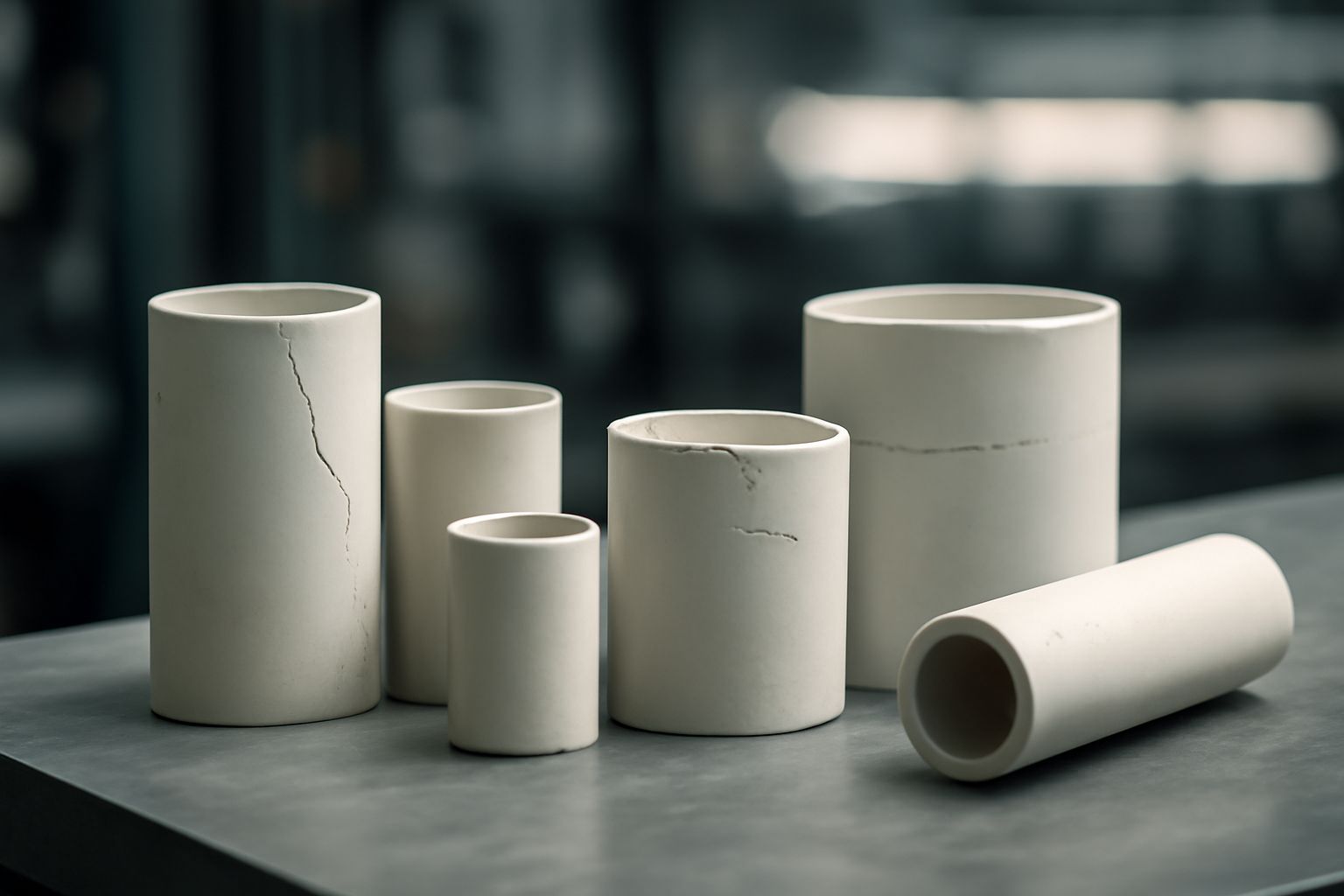
Qual abordagem de aquisição permitiu um retorno mais rápido dos protótipos?
Aproveitando a comunicação direta e o estoque pré-verificado de Fornecedores chineses de tubos de alumina é o fator crítico para acelerar os ciclos de entrega de protótipos. No meu recente projeto OEM, contornamos intermediários, contratando um fornecedor que oferecia estoque padrão e peças de tubo de alumina personalizadas . Isso permitiu a seleção imediata do material e o envio rápido das amostras.
Enviamos desenhos técnicos e tolerâncias dimensionais diretamente. Sem atrasos na tradução, sem "atraso de agência". O fornecedor forneceu uma folha de rastreabilidade de materiais e confirmou a disponibilidade para alumina de alta pureza acima de 99,5%. Nossa escolha de tubos "prontos para envio" e a usinagem CNC rápida simultânea de pequenos lotes permitiram uma Redução de 35% no tempo total de entrega do protótipo —reduzindo os ciclos típicos de 4,5 semanas para menos de 3 semanas.
Etapa de aquisição | Abordagem Tradicional | Otimizado (CSCERAMIC) |
---|---|---|
Método de sourcing | Mediado por agente | Fornecedor direto com estoque verificado |
Prazo de entrega da amostra do protótipo | Média de 4,5 semanas. | Média de 2,8 semanas. |
Rastreabilidade de materiais | Muitas vezes não especificado | Certificação de lote completo |
Como o suporte técnico otimizou a adaptação de máquinas automatizadas?
O envolvimento precoce da engenharia do fornecedor é a base para uma integração rápida e precisa de componentes de alumina em sistemas de automação. Em nossa experiência, o envolvimento de equipes técnicas chinesas durante a fase de DFM (Design for Manufacturability) nos permitiu ajustar a espessura da parede e otimizar as tolerâncias para montagens robóticas de alta velocidade .
Os engenheiros internos do fornecedor recomendaram a troca para um material com 99,7% de alumina para melhor desempenho dielétrico e maior resistência ao desgaste. Comunicamo-nos por videochamadas em tempo real e marcações detalhadas por e-mail, recebendo feedback completo em 2D/3D sobre as dimensões dos slots em 24 horas. Ajustes precisos significaram menos ciclos de tentativa e erro, reduzindo diretamente o tempo e o custo da remanufatura.
Recurso de suporte | Impacto | Exemplo / Fonte |
---|---|---|
Ajustes de DFM durante a cotação | Precisão de ajuste melhorada; revisões reduzidas | Visão geral do DFM |
Iteração CAD 3D | Ciclo de 24 horas, múltiplas atualizações de design possíveis por semana | Dados do projeto OEM (1º trimestre de 2024) |
Recomendação de material | 99,7% de alumina aumentou a vida útil em 23% | Aplicações cerâmicas (Kyocera) |
Quais verificações de qualidade garantiram um desempenho confiável após a instalação?
Uma inspeção completa — antes e depois do embarque — é essencial para uma implantação sem problemas em equipamentos automatizados. Nosso fornecedor implementou um rigoroso processo de IQC/OQC baseado na ISO 9001, incluindo Medição 100% dimensional e teste de rigidez dielétrica em cada lote de tubos de alumina.
Após a instalação, nossos testes de campo confirmaram zero falhas ou vazamentos após 5.000 horas de operação de alta frequência em manipuladores robóticos. A disposição do fornecedor em compartilhar dados de teste e certificados específicos de lote reforçou ainda mais os requisitos globais de rastreabilidade. A colaboração com produtores chineses que aceitam auditorias de terceiros, como SGS ou TÜV, adiciona outra camada de garantia, atendendo até mesmo aos rigorosos padrões dos mercados europeus.
Verificação de qualidade | Teste realizado | Resultado |
---|---|---|
Precisão dimensional | Laser CMM (±0,02 mm) | Aprovado, lote 100% |
Rigidez dielétrica | Teste de ruptura (>12kV/mm) | Passar |
Rugosidade da superfície | Teste Ra (≤0,8μm) | Passar |
Certificação de terceiros | Auditorias SGS/TÜV | Disponível |
Que lições os OEMs globais podem aprender com essa estratégia de terceirização?
A parceria antecipada com fabricantes chineses especializados em tubos de alumina proporciona aos OEMs globais uma vantagem em velocidade de prototipagem, eficiência de custos e colaboração técnica contínua. Os projetos mais bem-sucedidos contam com troca aberta de dados de engenharia, documentação de qualidade transparente e prontidão do fornecedor para ciclos iterativos rápidos.
Para compradores B2B em equipamentos de automação e robótica A capacidade de garantir tubos cerâmicos de alta pureza e acabamento de precisão sem longas interrupções no fornecimento é uma forte vantagem competitiva. Dados verificados, diálogo direto com a engenharia e rastreabilidade dos lotes garantem um escalonamento tranquilo — da amostra à produção em massa —, ao mesmo tempo em que atendem aos exigentes padrões internacionais. (ISO 9001) .
Lição Chave | Impacto para OEMs |
---|---|
Engajamento direto precoce | Tempo de lançamento no mercado mais rápido e designs mais robustos |
Transparência de qualidade | Preparação para auditoria para compradores globais |
Usinagem versátil e manutenção de estoque | Lacunas de fornecimento minimizadas durante a aceleração |
A escolha de fornecedores ágeis de tubos de alumina chineses pode reduzir os prazos do seu projeto de novos equipamentos, mantendo a confiabilidade no centro da sua cadeia de suprimentos.
Desbloqueie a prototipagem rápida e escale com parcerias com fornecedores baseadas na colaboração técnica e no controle de qualidade transparente.